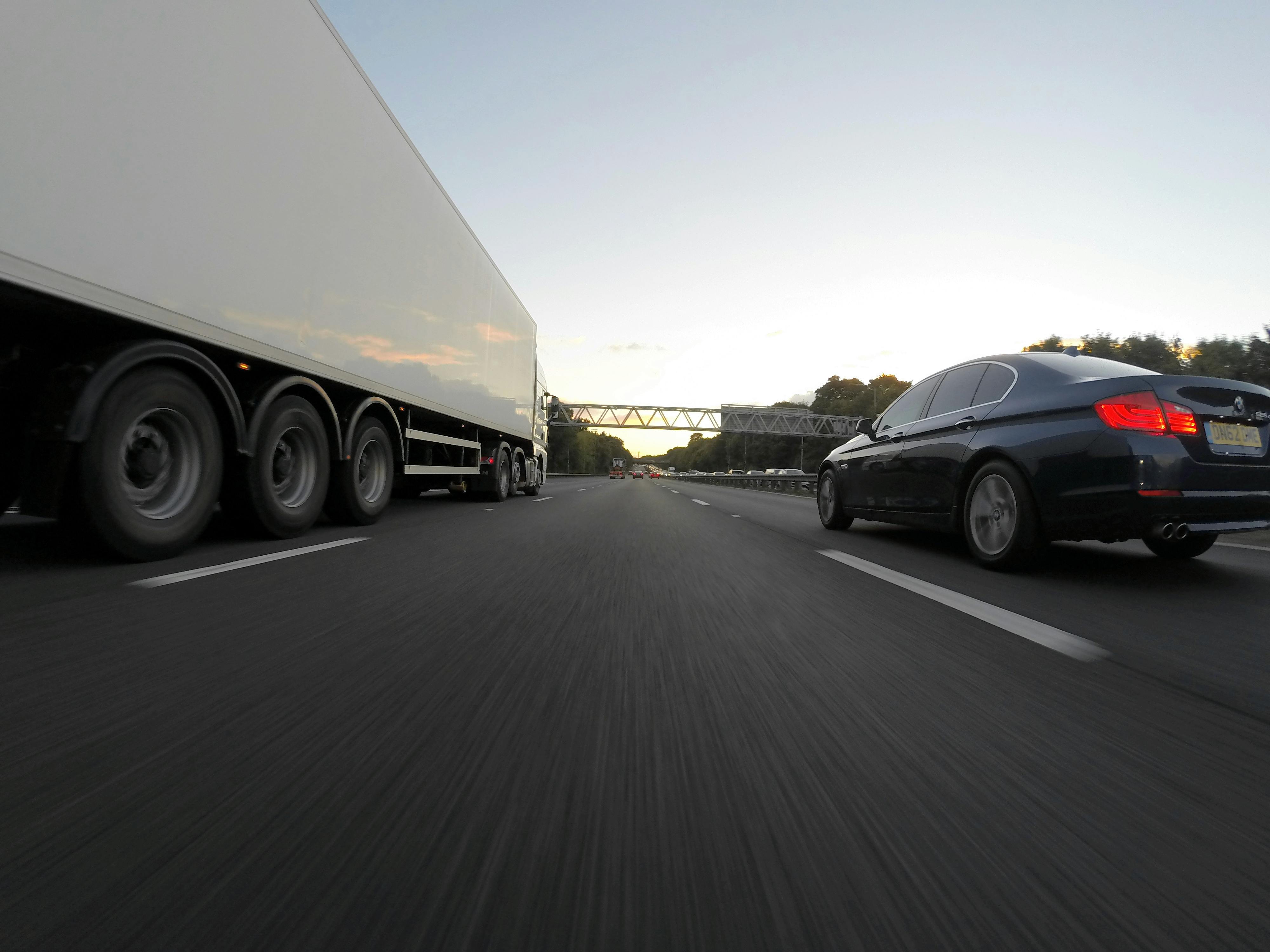
The axle configuration of any vehicle - whether a car, 4x4 van, rigid or articulated lorry, or even larger plant machinery - has a major impact on performance and operation. Understanding the different types of truck axles is therefore essential for making informed vehicle selection decisions. Axle configuration directly impacts load capacity, road regulations and vehicle performance across various applications. In this article, we'll explore these factors in detail to provide you with comprehensive information about the types of axles in trucks.
WHAT ARE TRUCK AXLES?
Truck axles are structural components that support the vehicle's weight, enable wheel rotation and provide a mounting point for suspension and braking systems. The number and arrangement of axles determine a vehicle's weight distribution, turning radius and overall road impact.
Different types of axles in trucks serve specific purposes based on their position, design and function within the vehicle. Each axle type contributes to the truck's overall performance characteristics and operational capabilities.
COMMON LORRY AND TRUCK AXLE TYPES
DRIVE AXLES
Drive axles transfer power from the engine to the wheels, propelling the vehicle forward. These axles connect to the transmission system through the driveshaft and differential. The key characteristics of drive axles include:
- Comprisal of differential systems for power distribution
- Often feature heavier construction to handle torque loads
- May include locking mechanisms for improved traction
- Typically rated for higher weight capacity than non-drive axles
Most rigid trucks use a single drive axle, while heavier articulated vehicles may feature tandem drive axles for improved traction and load distribution across challenging terrain or when hauling maximum legal weights.
STEER AXLES
Located at the front of the vehicle, steer axles control directional movement through the steering system. These axles pivot to change the vehicle's direction while supporting the front-end weight. Some of their most important features include:
- Typically rated for lower weight capacity than drive axles
- Connected to the steering mechanism for directional control
- Often use single-wheel configuration rather than dual wheels
- Incorporate specialised suspension designs for road handling
Proper steer axle maintenance is crucial for vehicle control and safety, particularly for long-haul operations where driver fatigue can be a factor. Weight distribution must be carefully managed to avoid overloading steer axles, which can compromise steering control.
TAG AXLES
Tag axles are non-powered additional axles positioned behind the drive axle. These axles provide extra load-bearing capacity without the mechanical complexity and fuel consumption of drive axles. Their primary benefits include:
- Increased legal payload capacity
- Improved weight distribution
- Better bridge formula compliance
- Reduced road surface impact
Tag axles often feature lift mechanisms that allow the axle to be raised when operating with lighter loads, reducing tyre wear and improving fuel efficiency. This versatility makes them popular for vehicles that operate with varying load weights.
PUSHER AXLES
Similar to tag axles but positioned ahead of the drive axle, pusher axles offer additional weight distribution and load capacity. These axles are common in specialty transport configurations where weight distribution is critical. Their better weight distribution and added stability for higher centre of gravity loads makes them perfectly suited for hauling specialised cargo. They also offer improved manoeuvrability compared to rear-mounted tag axles.
Pusher axles also frequently incorporate air suspension systems that allow for precise weight distribution adjustments based on load characteristics. This adaptability makes them valuable for specialised transport operations.
AXLE CONFIGURATION SYSTEMS
SINGLE AXLES
Single axles feature one axle at each position and are common in lighter commercial vehicles. This configuration offers simplicity, reduced maintenance and lower purchase costs. Applications best suited for single axles:
- Urban delivery vehicles
- Light to medium-duty transport
- Applications where manoeuvrability is prioritised over capacity
- Operations with consistent, moderate load requirements
Single axle configurations typically offer better fuel efficiency and lower maintenance costs for appropriate applications, making them cost-effective for suitable operations.
TANDEM AXLES
Tandem axles incorporate two axles positioned closely together, distributing weight more effectively while increasing load capacity. This configuration is standard on many heavy-duty commercial vehicles. Key benefits of tandem axles:
- Significantly increased load capacity
- Improved traction in challenging conditions
- Better weight distribution across road surfaces
- Enhanced stability for tall or high-centre-of-gravity loads
Tandem drive axle configurations are particularly valuable for operations requiring maximum legal payloads or when operating on varied terrain where additional traction is beneficial.
TRIDEM AXLES
Tridem configurations feature three axles grouped together, providing maximum legal payload capacity for commercial transport. These systems are common in heavy haul and bulk transport applications as they support the maximum legal payload capacity, offer superior weight distribution characteristics and are able to reduce ground pressure in sensitive terrain.
Vehicles with tridem axles typically require more sophisticated suspension systems to ensure proper weight distribution across all axles. These configurations are ideal for operations where maximising payload within legal limits are the primary objective.
SPECIALISED AXLE TECHNOLOGIES
SELF-STEERING AXLES
Self-steering axles automatically adjust wheel direction during turns, reducing tyre scrub and improving manoeuvrability for multi-axle vehicles. These axles are particularly valuable for long wheelbase vehicles operating in urban environments. The benefits of self-steering axles include:
- Reduced tyre wear on multi-axle configurations
- Improved turning radius for long vehicles
- Decreased road surface damage
- Enhanced fuel efficiency through reduced rolling resistance
Self-steering systems typically include centring mechanisms that return wheels to the straight-ahead position after completing turns, ensuring predictable handling during straight-line driving.
LIFT AXLES
Lift axles can be raised off the ground when not needed for load support, reducing rolling resistance and tyre wear. These versatile systems are available in both pusher and tag configurations.
Operational advantages of lift axles:
- Reduced fuel consumption when operating with lighter loads
- Decreased tyre wear during partial load operations
- Improved traction for drive axles in challenging conditions
- Enhanced manoeuvrability when navigating tight spaces
Modern lift axle systems often incorporate automatic load-sensing technology that deploys the axle when needed based on vehicle weight, optimising efficiency while ensuring compliance with axle weight regulations.
REGULATORY AND COMPLIANCE CONSIDERATIONS
WEIGHT REGULATIONS
Axle configurations directly impact a vehicle's legal carrying capacity. Different regions establish maximum weights per axle and overall gross vehicle weight based on axle spacing and total axle count.
In the UK, standard drive axles are typically limited to 11.5 tonnes, while steer axles are usually restricted to a maximum of 8 tonnes. These individual limits combine with overall vehicle weight restrictions to determine legal payload capacity.
Understanding key regulatory factors including individual axle weight limits, tandem and tridem axle group weight allowances, bridge formula calculations, and seasonal weight restrictions is essential for specifying vehicles with axle configurations that maximise legal payload capacity.
BRIDGING FORMULA COMPLIANCE
Bridge formula regulations protect infrastructure by establishing weight limits based on axle spacing. Proper axle configuration ensures maximum legal payload while maintaining bridge formula compliance.
Compliance considerations include axle spacing measurements between axle groups, total vehicle wheelbase for weight calculation, inner bridge dimensions for multi-axle configurations, and special permits for non-standard configurations. Axle configurations designed with bridge formula compliance in mind enable operators to maximise payload capacity while remaining within legal weight parameters.
OPERATIONAL IMPACT OF AXLE SELECTION
FUEL EFFICIENCY
Axle type and configuration significantly impact fuel consumption. Additional axles increase weight and rolling resistance, while appropriate configurations optimise load distribution and operational efficiency.
Key factors affecting efficiency include the number of ground-contacting axles, proper matching of axle weight ratings to actual loads, strategic lift axle utilisation, and appropriate drive axle ratio selection. Carefully matching axle configuration to typical operating conditions can yield substantial fuel savings over a vehicle's service life.
MAINTENANCE REQUIREMENTS
Different axle types present varying maintenance needs and service intervals. Understanding these requirements is essential for effective fleet management and cost control.
Essential maintenance considerations include specific lubrication requirements for each axle type, appropriate inspection schedules for steering components, regular air system maintenance for lift axles, and proper alignment specifications for multi-axle configurations. Developing maintenance protocols specific to each axle type helps ensure reliable operation and maximum component lifespan.
HOW TO CHOOSE THE RIGHT AXLE CONFIGURATION
Selecting optimal truck axle types involves assessing several operational factors:
- Typical payload weight and distribution
- Common operating terrain and conditions
- Manoeuvrability requirements for delivery locations
- Regional weight regulations and enforcement patterns
The ideal axle configuration balances maximum legal payload capacity with operational efficiency and purchase cost. Many operators benefit from working with experienced transport consultants to determine the most appropriate specification for their particular requirements.
FINDING YOUR IDEAL CONFIGURATION
There's no one-size-fits-all answer to axle selection. The right configuration for your operation depends on balancing multiple factors:
OPERATIONAL PRIORITIES
What matters most to your business? Maximum payload capacity? Fuel efficiency? Purchase price? Maintenance simplicity? Your priorities should guide your configuration choices.
APPLICATION SPECIFICS
A concrete mixer with its high centre of gravity and frequent off-road access has dramatically different requirements than a curtainside trailer doing regular motorway deliveries. Be specific about your application when configuring axles.
REGIONAL CONSIDERATIONS
Not only do weight regulations vary by region, but road designs, typical routes and even weather conditions can influence optimal axle selection. A configuration perfect for flat motorway routes might be problematic in mountainous terrain.
The most successful operators take a holistic approach, considering the entire operational picture rather than focusing on isolated specifications. This comprehensive view leads to better-performing vehicles and stronger financial results.
CONCLUSION
Given the complexity of axle configuration decisions, working with knowledgeable specialists often provides the best results. Our team here at Law Trucks' can help you in matching axle configurations to your specific operational requirements.
With decades of combined experience across diverse transport applications, our advice can help you navigate the complexities of truck axle types and configurations. Contact our team to discuss your specific operational needs and discover the ideal axle setup for your transport requirements.